Selecting the Right Industrial Lighting, Part 1
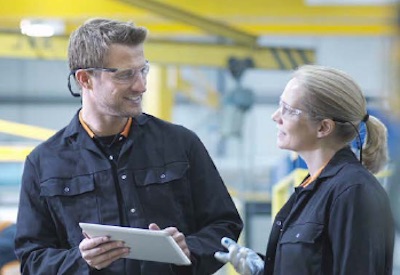
February 15, 2018
The rapid rise of LED lighting as a viable option for commercial and industrial applications has flooded the market with a wide array of products and information. This can create confusion among specifiers. In response, this white paper was produced by Eaton to raise awareness around LED luminaire capabilities for industrial environments and the considerations required for each application. It outlines the changing evolution of LED lighting and the many factors that decision-makers should look to address when considering such a large investment. Here in Part 1: two major reasons why lighting matters. In the next instalment: nine factors to consider in the selection process.
Lighting for industrial workplaces
Over a century on from Thomas Edison’s introduction of the commercially viable incandescent light bulb, it is easy to take lighting for granted. We live in an age where buildings can be illuminated around the clock without a second thought. This can be especially true of industrial settings, where consideration of lighting has traditionally taken a back seat to the more urgent demands of round-the-clock production schedules and tight control of costs. However, those who fail to recognize the important role of lighting in industrial environments may be missing out on significant gains. In manufacturing, warehousing, power generation and other industrial workplaces, a properly commissioned lighting scheme can enhance the wellbeing and productivity of employees, which has a contributory influence on the quality of their output. Additionally, significant cost savings can be secured by selecting the most efficient solution based on a given building, its occupancy and its primary functions. Thirdly, continuity of production can be supported by reliable and consistent lighting schemes that are sufficiently robust to withstand harsh working conditions.
The challenge lies in trying to gain an understanding of the available options. Lighting replacements and upgrades may only arise on the management agenda approximately every decade. At the same time, the technology of lighting has advanced beyond recognition in recent years, most notably with the rise of LED luminaires, which have arrived with a raft of new specification criteria. Given these conspiring factors, business and facilities leaders could be forgiven for approaching lighting decisions with a degree of trepidation.
Changing technologies
For a long period of time, low bay lighting was favoured in industrial buildings for its low cost and simplicity. High intensity discharge (HID) lamps were prevalent in this category. Compared with the sophisticated luminaires available today, these were relatively rudimentary devices, incorporating either mercury, metal halide (a combination of mercury and halogen) or SON (sodium) gases that facilitate the creation of an electric arc between two electrodes. However, HID lamps suffer from shortcomings that limit their efficacy, lifespan and safety. In some cases, they can take between 5 and 10 minutes to produce their stated output, due to the slow process of building up the required level of gas pressure internally. Equally, after being switched off, they cannot be immediately switched back on as the necessary cooling and reheating processes take time to complete. This has historically been problematic in brief instances of power failure, for example.
Towards the end of their lives, HID lamps can fail in problematic ways, either requiring larger voltages to maintain their arc discharge or, in some cases, exploding due to the deterioration of components caused by thermal stress, mechanical vibrations or the involvement of chemicals. Disposal can also be challenging, particularly for lamps containing mercury, which require specific safety procedures to be followed.
Replacement of such lamps with LED luminaires can be enormously beneficial for organizations aiming to maximize productivity by creating a comfortable and correctly lit working environment, while also achieving energy and cost efficiencies. An LED luminaire typically uses 50-60% less energy than a traditional light source, such as a fluorescent or HID lamp. However, it is worth noting that such performance depends on the use of luminaires incorporating high-quality LEDs and associated electronic drivers, plus excellent thermal management characteristics and optimised optical distribution.
To ensure optimum lighting arrangements, a number of important considerations need to be applied, ranging from detailed interrogation of product specifications to careful assessment of application-specific criteria including distribution of light, colour rendering and resistance to harsh environmental conditions. This series of articles seeks to explore these considerations in order to help the owners and managers of industrial buildings, along with the contractors, consultants and specifiers who support them to select the most suitable lighting scheme.
Why lighting matters
- Productivity. Properly designed and carefully implemented lighting schemes can have a beneficial effect on the wellbeing and productivity of employees, which in turn creates a platform for business growth. This is one of the major benefits of a properly designed lighting scheme, but often becomes a secondary consideration in the quest for energy savings, which have been amplified by the rise of LED technologies that enable relatively simple cost reductions.
Employers increasingly recognize the duty of care they have towards their employees and a consideration of staff needs is vital for morale. What’s more, forward-thinking businesses recognize that employees are more likely to be at the top of their game when they are immersed in a comfortable and stimulating environment.
This can include a well-designed workstation, a comfortable office temperature and appropriate lighting. Demonstrating this duty of care will undoubtedly foster a greater sense of staff satisfaction, increase motivation and productivity and lead to more staff retention. All of which ultimately contributes to driving up company profits.
Improved lighting is an essential element in the overall mix. In its guidance to employers, the Health and Safety Executive recommends that lighting should be considered principally at the design stage, but it also emphasizes the importance of ensuring the lighting is suited to the specific tasks being carried out, which may evolve over time.
A growing body of research underlines this important link between lighting and wellbeing. Lighting for People, a research paper that was produced as part of the European Union’s program for research and technological development, has drawn together a wealth of research to demonstrate just how important lighting is on human health and wellbeing.
For instance, Karin CHJ Smolders and Domien GM Beersma from the Department of Chronobiology at the University of Groningen in the Netherlands report that: “Workplace lighting can, in addition to providing sufficient light to conduct work-related visual tasks, affect employees’ alertness, mood, cognition, sleep-wake pattern and health.”[1]
However, this area of academic research is not a new phenomenon. As long ago as 1977, a study by Bennett, Chitlangia and Pangrekar demonstrated that when illuminance was increased, individuals took less time to carry out simple tasks such as map reading, probing needles and measuring the diameter of bolts.[2]
It goes without saying that a properly illuminated working environment can also enhance physical safety, particularly in hazardous industrial facilities where good visibility can reduce the likelihood of accidents involving heavy plant and machinery.
For all of these reasons, lighting replacement and upgrade projects should ideally prompt the establishment of stakeholder groups or committees comprised of business and facilities leaders and staff, all of whom may have their own perspectives on lighting requirements.
- Energy usage. Energy efficiency today is a major factor in the decision-making process for industrial, warehousing and manufacturing operations, as a result of rising energy costs, regulatory pressures and widespread expectations of environmental performance.
In large facilities such as factories and warehouses, lighting can consume as much as 50% of the total electricity bill, so it’s unsurprisingly a prime target for efficiency savings. Where lighting systems are 15 to 20 years old, the adoption of newer technology can bring the running cost of lights down by 50% or more.
This is one of the major reasons why LED lighting has risen up the purchasing agenda in recent years. Once considered a premium product carrying a restrictive upfront cost, LED luminaires are becoming more prevalent by the day thanks to advances in affordability and availability.
The appeal of LED lighting lies in its highly efficient ability to generate more light per unit of electricity than almost any other available technology.
In terms of their lifespan, they last up to 50 times longer than a conventional incandescent lamp and around five times longer than a compact fluorescent energy-saving light bulb.[3] For busy industrial applications, the reduced regularity, cost and disruption of maintaining lighting is a considerable advantage.
High-brightness LEDs are relatively expensive to produce because of the precise production techniques involved in the manufacturing process. However, the comparatively higher initial outlay must be weighed against the total cost of ownership, which is typically much lower than conventional lighting because of the inherent energy savings and reduced requirement for maintenance and replacement bulbs. In many cases, the payback period can be remarkably short. Again, this is dependent upon the purchase of properly engineered LED lights used in luminaires that are designed and built specifically for the purpose.
Having considered both the role of lighting in the workplace and its contribution to capital costs and overheads, let us now look at some of the specific considerations that apply to the selection process.
In Part 2: nine factors to consider in the selection process. In Part 3: 10 key questions to ask suppliers.
Graham White is a lighting technical manager at Eaton. This series of articles is based on a white paper published by Eaton. Read the paper in its entirety: http://electricalsector.eaton.com/en-gb_industrial_lighting_solutions_whitepaper
Notes
- “Lighting for health and well-being in education, work places, nursing homes, domestic applications, and smart cities” by Accelerate SSL / Innovation for Europe. First published in 2014. http://lightingforpeople.eu/2016/wp-content/ uploads/2016/03/SSLerate-3.2-3.4-v4.pdf
- “Illumination Levels and Performance of Practical Visual Tasks” by Corwin A. Bennett, Anand Chitlangia, Abhay Pangrekar. First published in 1977.
http://journals.sagepub.com/doi/abs/10.1177/107118137702100413?journalCode=prob
- The Lighting Industry Association Consumer Guide to LED Lighting, www.thelia.org.uk