12 Myths Surrounding Industrial LED Lighting, Part 1
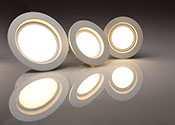
October 12, 2016
LEDs have been in widespread use for more than a decade, lighting everything from traffic signals and cell phones to computers and TVs, due to their extremely low energy use, long life span and high-quality light. While not new, LEDs now offer unique and compelling characteristics for industrial applications. LEDs are more durable, reliable and lack the maintenance requirements (e.g. re-lamping, re-ballasting) associated with traditional lighting. With properly designed fixtures, LEDs:
– can operate well in all temperature environments,
– are inherently controllable (instantaneous on/off and dimming)
– are much more energy efficient
Traditional industrial light sources share few, if any, of these characteristics. This is because, unlike high-intensity fluorescents (HIF), high-intensity discharge (HID), high-pressure sodium (HPS) and metal halides, LEDs are semiconductors, not light bulbs.
This fundamental difference is the source of many of the misconceptions surrounding LEDs. The challenge now is that the outdated evaluation criteria, which were applicable to legacy lighting, are still in use. So, it’s time to delve into those myths and look at the underlying facts.
Here are the first 6 of 12 myths. Watch for the second 6 in an upcoming issue of EIN.
1. LEDs are not a cost-effective replacement for fluorescents
FACT: LEDs are excellent replacements for fluorescents, HIDs and other industrial lighting.
While initial purchase costs for LEDs are higher than fluorescents, the price difference is a fleeting issue, at best. Unlike past decades, when lighting-related energy costs played a relatively small role in purchase decisions, a decade of rapidly escalating energy prices has transformed energy use into the major cost driver for industrial lighting.
Because intelligent LEDs are dramatically more energy efficient than fluorescents or even plain LEDs, not only are they more cost-effective in current terms, but an imperative in a rising-energy-cost environment. As a result, many industrial organizations are no longer willing to trade off marginally shorter initial payback periods—usually measured in months, not years—for a decade or more of substantially higher energy costs. From a purely financial perspective, it no longer makes sense. Factor in the elimination of maintenance and mercury disposal costs, and the advantages of LEDs are overwhelming.
For example, if you compare the annual energy costs of a 100-fixture installation of 6-lamp T8 HIF vs. a 13,000-lumen Intelligent Lighting System in a $0.10 kWh area with 20% occupancy, the comparison is as follows:
6-Lamp T8 HIF |
13,000-Lumen Intelligent Lighting System |
|
Annual Energy Costs | $17,432 | $2,715 |
5-Year Energy Costs | $87,160 | $13,575 |
The 5-year energy costs for the LED-based Intelligent Lighting System are less than a single year’s energy costs for the HIF. And LEDs have no ongoing maintenance requirements (re-lamping or re-ballasting).
2. LEDs are too new of a technology
FACT: LEDs have been in widespread use for more than a decade, including critical safety-related applications.
Following more than a decade of widespread use, LEDs are a mature, reliable technology that has earned its place in the mainstream lighting market. LEDs’ surging popularity is based on their unique ability to provide dramatically more energy-efficient, sustainable and cost-effective lighting. By combining much greater flexibility and control over how lighting is used within a facility, with higher quality light, LEDs are rapidly becoming the illumination technology of choice for industrial applications. Their customer-proven durability is well suited to high-intensity industrial applications, including manufacturing, warehousing, maintenance depots, hangars, and numerous others.
3. LEDs have magnetic ballasts that require servicing and/or replacement
FACT: LED lights use electronic drivers, which don’t need replacement.
A magnetic ballast is an electrical circuit that regulates the amount of current that passes through a gas discharge light, controlling both the starting and operating voltages. Over time, magnetic ballasts used in traditional industrial lighting (HID, HIF, HPS, metal halide) wear out, requiring servicing and/or replacement. For large industrial facilities with hundreds of fluorescent or HID fixtures, servicing ballasts is an expensive proposition — in terms of manpower, workplace disruptions and component replacements.
LEDs are semiconductors that efficiently generate light, and require electronic drivers. In a well-designed fixture, the driver is a critical component, managing the power delivery and playing a vital role in overall energy efficiency of a fixture. It is a key element in fixture power consumption per lumen delivered, heat generation, and longer fixture lifetimes. Because LEDs use electronic drivers, they provide LED manufacturers with the opportunity to integrate control features (e.g. sensing, dimming and instantaneous on/off) into lighting fixtures for maximum functionality and efficiency.
4. LED prices will go down, so it pays to wait
Fact: Waiting for LED fixture prices to drop will cost you money.
The energy savings from upgrading a facility’s lighting to LEDs far exceed any incremental price declines in LED-based fixtures.
The major factors associated with industrial lighting are up-front costs and energy use, making the frequently cited comparison between computer processing chips and LEDs inappropriate. Yes, LED chips are declining in price, but much of the cost of LED lighting is in the system that is built around that chip, so the potential chip price decline only impacts about 1/3 of the fixture.
A quick glimpse at a typical facility’s operating budget shows that lighting is one of the largest energy loads. By reducing that energy usage 50% to 90% (depending on the application and manufacturer), LEDs pay back in energy savings much more than could ever be accrued through incremental LED price declines. If anything, energy’s upward price trend makes waiting even more costly. It does not pay to wait. It does pay to act.
Using the same $0.10/kWh rate, for example, a single 6-lamp T8 fixture typically consumes $174 in lighting-related energy costs per year. An intelligent LED fixture consumes just $27, resulting in a net savings of $147 per year (not including the additional daylight harvesting, maintenance and/or refrigeration savings associated with intelligent LEDs). This means that the cost of an LED fixture would have to drop dramatically in a single year to make waiting worthwhile.
5. LED drivers require replacement
FACT: Well-designed LEDs should not have driver failures.
During the usable lifetime of an LED, which generally exceeds 50,000+ operating (or “on”) hours (or more than twice the lifetime of a traditional light source), it is extremely unlikely that a driver or any other component part would need to be replaced. Furthermore, in a well-designed LED fixture, frequent on/off switching does not shorten its useful life, unlike traditional fluorescent or HID lighting fixtures whose useful lifetimes are significantly reduced by such operations. In fact, frequent switching actually lengthens the useful life of an LED, as turning off an LED fixture slows the pace at which total operating hours accrue.
6. LEDs contain mercury
FACT: LEDs do not contain mercury.
Unlike fluorescents, LEDs do not contain mercury, a hazardous material with high disposal costs, and which is dangerous when used in food-related environments, in particular.
The remaining 6 myths will appear in an upcoming issue.
Conclusion
Interest in LED lighting is at an all-time high as industrial facilities increasingly zero in on energy efficiency, sustainability and cost containment as key metrics for capital investment decisions. Given the importance of these metrics to a facility’s bottom line and long-term competitiveness, few question that LEDs will soon become the lighting technology of choice in the industrial sector. The key is for customers to become knowledgeable about LEDs — with accurate information, independent test data, and feedback from the growing base of real-world installations willing to talk about their successes. Be sure to ask any industrial LED lighting company you speak with for full test results (LM-79, LM-80 and TM-21), and relevant listings (UL, cUL, NOM, or CE, for example).
This article was first published online by Digital Lumens.