Improving the Heat Sink in Modern LED Fixtures
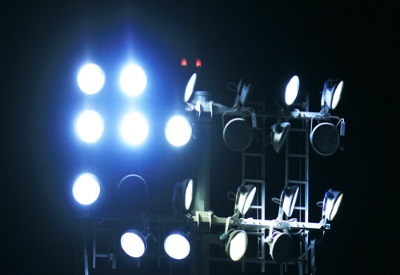
Many people understand that LED lighting uses fixtures that are cooler to the touch than traditional incandescent light bulbs. LED lights do not generate light in the infrared spectrum and are, in fact, both cooler and more efficient than incandescents. Unlike traditional light bulbs that typically convert less than 10% of electrical energy input into illumination, LED fixtures can convert up to 45% of electrical power input into light. The remaining power is dissipated as heat, which requires heat sinks and other thermal management techniques in order to maintain the integrity and quality of the LED fixtures. Among LED lighting engineers, improving the heat sinks in LED fixtures is a predominant focus of modern LED lighting technology.
Heat Sink Technology in Modern LED Fixtures
Heat transfer from an LED fixture occurs through both conduction and convection. Excess heat is conducted away from the LED junction and into a heat sink that is attached to the LED. That excess heat is then dissipated into the surrounding air through convection as air flows past and around the heat sink. This convective cooling improves when the heat sink has greater surface area, as more surface area correlates with a greater volume of air flow to remove excess heat. Improving the heat sink is therefore a matter of improving the attachment of the sink to the LED to improve conductive cooling, and increasing the surface area of the sink for better convective cooling.
Initially, even a heat sink with a large surface area will be ineffective if heat is not properly conducted into it. The connection between a heat sink and an LED will act more as a thermal insulator and not as a conductor if that connection is not engineered properly. Any air pockets in that connection will impair conduction, as will materials that are not effective conductors or transmitters of heat. Likewise, LED manufacturers need to use heat sink materials that minimize internal air pockets that could impede the transfer of heat away from the LED.
The design of the heat sink will, in part, be limited by the shape and geometry of the LED fixture. Within those limitations, engineers have designed heat sinks with double-folded fins. They also use materials, like aluminum, that are pliable and easy to shape without any loss in their effectiveness as heat conductors. SpecGrade LED, a domestic designer and manufacturer of commercial and industrial LED lighting systems, has developed a patented heat sink technology that incorporates these and other features, such as a proprietary thermal bonding technology.
Next Generation Thermal Management Technology
Most LED lighting technology relies on passive cooling, rather than on fan-assisted or other active cooling methods. Fins on a heat sinks that are used in passive cooling systems are often designed to take advantage of strategic airflow and air pockets within an LED fixture. Warmer air naturally rises, creating small air currents around an LED. SpecGrade LED and other companies work with this natural airflow and design their heat sinks with aerodynamic fin shapes and other features that capture as much airflow as is possible regardless of the orientation of the LED light fixture.
Unless and until LED lighting engineers have determined how to convert 100% of all electrical input energy into usable light, thermal management of LED fixtures will be mandatory to reduce thermal stress on an LED fixture’s components and to extend the useful life of the fixtures.
https://www.specgradeled.com/improving-heat-sink-modern-led-fixtures/