Luminaire-Integrated Lighting Controls
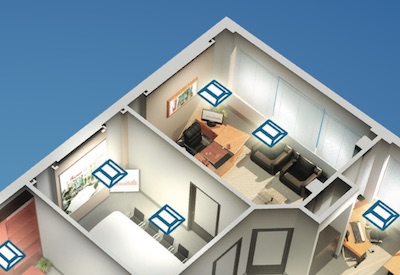
May 4, 2018
A relatively recent trend in the industry is to embed “luminaire-integrated” (embedded) controls into each fixture. This can be done in different ways, with different types of components, and with different types of control systems.
The most basic version of luminaire-integrated controls consists of on-board sensors that tell the fixture what to do — without getting into the complexity of a networked lighting control system. In other words, each fixture operates independently based on input from its own onboard sensors. Most often these are occupancy sensors. However, many fixtures also have options for built-in photosensors (daylight sensors).
One of the benefits of this type of approach is that it is relatively simple to specify, purchase, install and commission. Additionally, if the fixture vendor can pre-install the control components, then the electrical contractor doesn’t have to connect any additional wiring on the job site. Any connections for 0-10V or DALI wiring or any other low-voltage wiring such as from the sensors to the controller can be made in advance in the fixture vendor’s factory.
While this approach may seem like the most logical choice from the viewpoint of ease of specification and installation, and the lowest cost option, there are limitations that should be considered. For starters, if the control components are not networked, then there’s no way to monitor what is happening with the lighting installation. That means that there’s also no way to monitor energy usage.
When using “stand alone” embedded controls on a per-fixture basis, there are typically limited or even predetermined options for how the controls behave. For example, new LED high-bay fixtures may be specified for a warehouse with fixture-integrated controls, including occupancy sensors. Some vendors offer these in “high-low” versions. While the sensors may detect occupancy or vacancy exactly the same way as any other occupancy sensor, the associated circuitry may only allow the fixture to toggle between 100% and 10% light output. That’s a great strategy for saving energy in warehouse aisles, and that may even be mandated by the applicable energy code. However, if the circuitry doesn’t allow the fixture to actually turn off when the sensor detects vacancy, then it won’t meet the “automatic shutoff” requirement in almost all energy codes.
One way to solve this problem and comply with the code requirement for automatic shutoff is to install a relay panel with a time-clock function upstream of the fixtures and turn the circuits off after hours. Of course, once you do that, the embedded occupancy sensors will not be able to turn the lights on in the event that someone comes in after hours because the sensors won’t work if the fixture isn’t getting power. Very complicated! Additionally, there’s no way to program or reprogram variables for embedded controls either globally or individually without getting on a ladder and accessing the embedded controls in situ — at every single fixture — assuming that there are options for changing any of the settings on particular control devices.
Increasingly, “networked” lighting control systems are being specified and installed. This means that all components either speak to a central server or to each other. Of course, you can still specify a networked lighting control system that doesn’t have sensors or controllers in every fixture. Controllers (consisting of a relay to turn the fixture on or off, as well as circuitry to provide a 0-10V or other signal to dim the fixture up or down) can in fact be installed on a per-circuit or per-switch leg basis, upstream of the fixtures they are controlling. Occupancy sensors and photosensors can be installed in locations that are independent of the fixtures. In that case, the sensors must be linked either wirelessly or via wires to the fixtures, or at the very least to a central server. This depends on the topology of the system and how it handles transmission of information through its network.
Even in a networked lighting control system, there are still additional benefits of using fixture-integrated (embedded) control devices on a per-fixture basis. One of the biggest benefits is that zoning — and for that matter rezoning — is determined by grouping fixtures together via software, not based on wired circuits or switch legs. This provides the maximum flexibility for the owner who is free to configure and reconfigure zones of fixtures at any time.
Another benefit of using fixture-integrated devices in a networked control system is that there is greater granularity of coverage from occupancy sensors. It’s likely that the greater granularity of coverage from on-board occupancy sensors will lead to the biggest decrease in energy usage in a given space. As an example, a ceiling-mounted occupancy sensor with an omni-directional coverage pattern of 1,500 sq.ft. should detect people in a circle with a diameter of 44 ft. If a fixture-integrated occupancy sensor has a coverage pattern of 200 sq.ft., then it would detect people in a circle with a diameter of only 16 ft. The smaller the coverage pattern, the more likely that some fixtures will dim down or turn off during the day.
There are other potential benefits to deploying controls on a fixture-integrated basis even with a networked system. For example, some vendors offer multi-sensors that not only contain PIR occupancy sensors and photosensors, but also temperature sensors. This can allow the lighting control system to create a heat map (literally and figuratively) of the temperatures throughout a space. This information might be passed through to the HVAC system so it can make appropriate adjustments, or monitored by the building engineer who can then do so manually.
Lighting control system vendors are also starting to experiment with using fixture-integrated controls to pick up other types of data. For example, if the fixture-integrated controls and sensors are deployed in a manner where each fixture directly correlates to one occupant, the owner can build up information about space usage throughout the facility. This could be used, for example, to tweak the programming of the HVAC system to mirror the actual use of the space on a much more granular basis, or to verify the typical number of days when employees are out sick. Another potential benefit to deploying controls on a fixture-integrated basis is asset tracking. Equipment can be “discovered” by the sensors in each fixture so the owner always knows where everything is.
Remember that once all components of a lighting control system are networked, that enables many of the benefits that are denied to standalone embedded controls. Fixtures and energy usage throughout a facility can be monitored on a granular basis. Behaviour of fixtures and sensors can be changed via software either globally or individually. Assuming that the control system allows it (which most do), different behaviour can be established for the same equipment at different times of the day or for different days of the week.
Lastly, do not forget that whatever type of controls you specify, ask the vendor up front how emergency lighting works with their equipment. Every non-residential project must have some means of providing fail-safe emergency egress lighting.
Published with the permission of Lighting Control Association.
Steven Mesh is an award-winning lighting designer who has designed lighting and control systems for a variety of project types (commercial, museums, schools, residential, restaurants, retail, historic, healthcare, etc.). As an educator, he has taught classes and given presentations about lighting and controls across North America and internationally. One of his is developing lighting and lighting controls courses that rely on hands-on and/or interactive content. He has been a repeat speaker at LightFair for many years.
Image source: Cree Canada