Case Study from Cooper Lighting: Aerospace Manufacturer
November 29, 2023
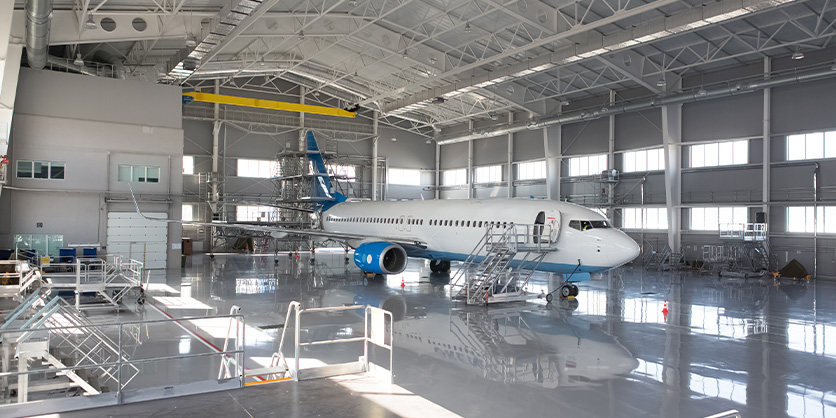
Background
Cooper Lighting’s customer is a leading aerospace manufacturer that produces the fuselage and other major components for airliners.
The company’s headquarters is in Wichita, Kansas, known as the “Air Capital of the World” due to the predominance of aerospace manufacturers in the area.
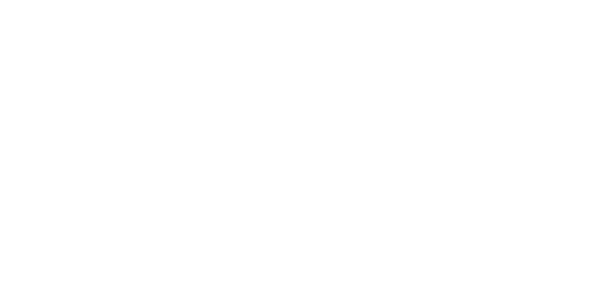
Challenge
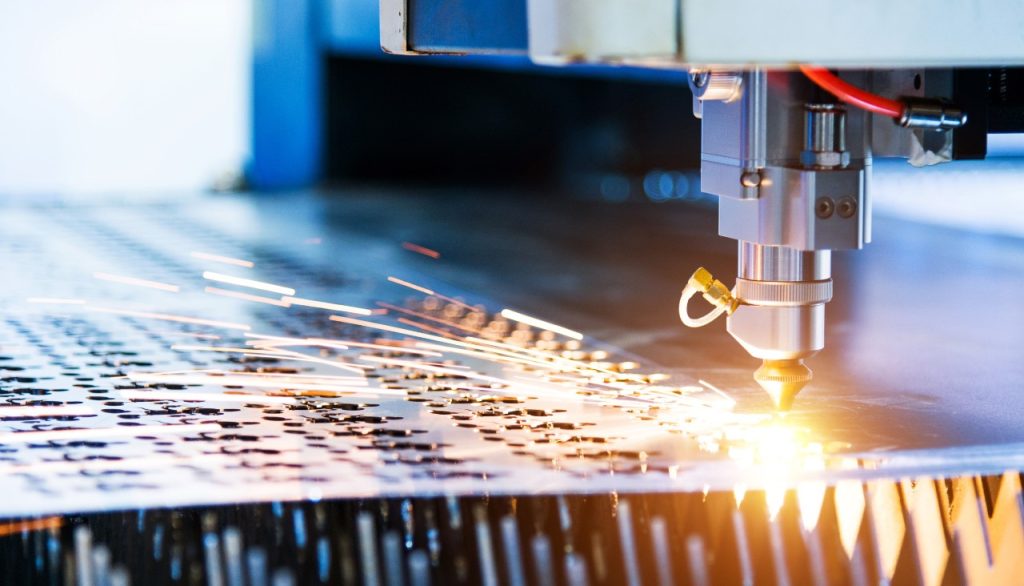
This aerospace manufacturer was looking to retrofit the lighting in 17 facilities on its campus. That equaled a combined area of 11 million square feet (under roof).
The new lighting had to be bright enough – from 45 – 50 feet above the facility floor – so each worker had ample light to perform the task required. Specifically, the new fixtures had to meet the 80FC aerospace industry production standard.
It was decided the manufacturer needed to redesign their lighting and replace their legacy 1000W HID lighting fixtures with LED lighting.
Cooper Lighting Solutions was also asked to update the outdoor lighting illuminating the roadways and parking lots of the aerospace manufacturer’s campus.
And, like most manufacturers, this customer wanted to maximize the energy cost savings that would result from the new fixtures.
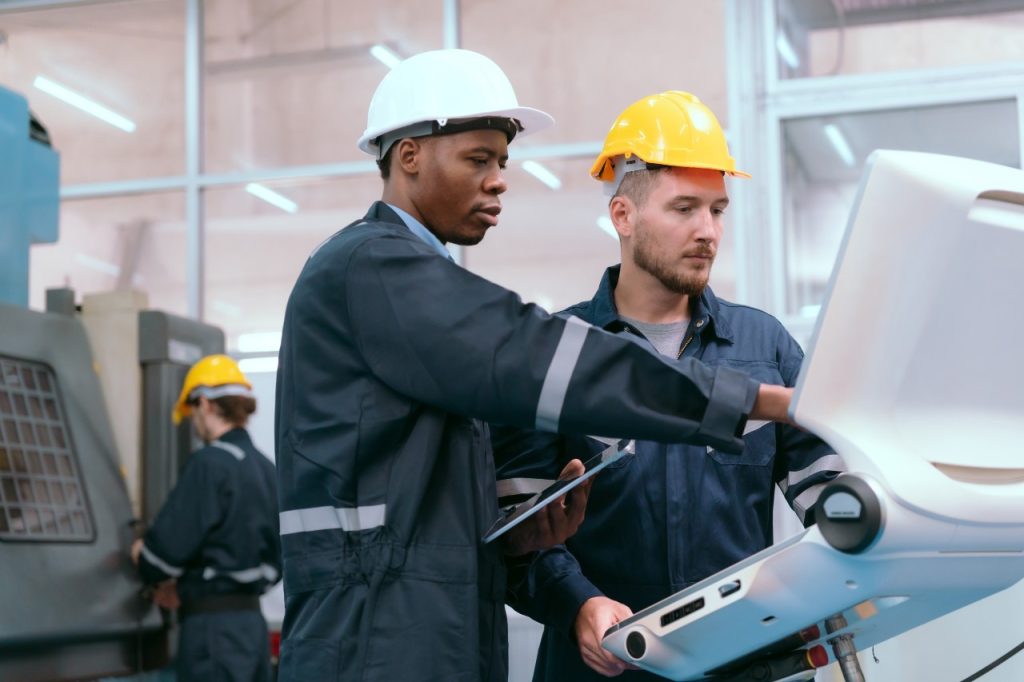
Solution
Cooper Lighting Solutions retrofitted the aerospace manufacturer’s 20,000 existing fixtures and added a new wireless connected lighting control system.
The new energy-saving LED fixtures included high bays, linear bays, and floodlights from the extensive and innovative product offering from Cooper Lighting Solutions.
Results
In the manufacture of major airliner components, there’s no room for error, so appropriate lighting on the facility floor is a necessity. Cooper Lighting Solutions delivered.
Energy and cost savings.
Today’s LED fixtures can provide up to 80% cost savings over traditional lighting. And because LED fixtures last up to 12 years before needing to be replaced, they help lower maintenance costs.
Noticeably brighter light.
Because of higher lumen output, better optical distribution, and precision optics, the new fixtures produced higher footcandles with less wattage.
Increased worker safety.
In a manufacturing facility, high-quality, uniform light that produces less glare – like that which Cooper Lighting Solutions fixtures provide – results in improved visual comfort and decreased eye strain for workers, which in turn helps lower the risk of workplace accidents.
High product quality.
High-quality, uniform light also helps provide workers with the illumination they need to do their best work and produce fewer mistakes.
Cooper Lighting Solutions is continually improving and updating its product lines to reflect lighting innovations and other advancing technology.
As a result, the products used in this project (completed in 2017) have already been updated with new features and benefits for Cooper Lighting’s manufacturing customers. The products displayed below are from the current Cooper Lighting Solutions offering and are comparable to those used in this project.
Products Used
7,920 High Bays
790 Linear Bays
465 Low Bays
2,064 Troffers
2,095 Strip Lights
65 Area/Site Luminaires
More information available here
Related Article
5 Specifying Tips from Cooper Lighting: Designing Parking Lot Lighting for Healthcare Facilities
Hospital and other healthcare facility parking lots have their own special challenges when it comes to lighting. You have emergency vehicles racing in and out. Cars frequently pulling in and out of parking spaces. A good number of pedestrians during evening hours, many of whom are older or infirm