How to Detect Problems In Your Warehouse Using Artificial Intelligence
November 15, 2023
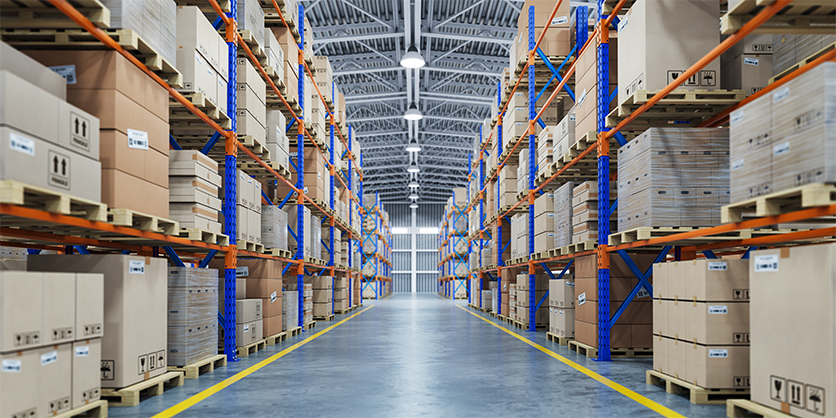
David Gordon
Warehousing is core to a distributor’s value proposition. Customers expect distributors to carry inventory. The 2023 NAED PAR report (2022 data) stated that, on average, 72% of distributor sales emanate from their warehouse.
Given the importance of a warehouse to distributors, managing costs and reducing errors is critical to profitability. And accuracy is important to customer satisfaction.
Again, from the NAED PAR report, 1.7% of distributor operating expenses is allocated to warehouse with 1.3% being allocated to labor, hence labor is 76.5% of warehouse operating expenses.
This means that managing warehouse productivity is important.
Given this, Dick Friedman shared some ideas on how AI could help distributors improve warehouse productivity and accuracy.
“A previous article shared some ideas on how Artificial Intelligence (AI) could be beneficial in a distributor’s warehouse and how it could recommend a target warehouse accuracy level. Further, it could determine if a warehouse worker is as productive as she/he should be.
This article describes how AI can determine if your warehouse storage arrangement (how you layout what goes where) has been causing mistakes that could result in lost sales and perhaps customers; and if the arrangement is reducing productivity and the costs of that reduction
The logic for these determinations can be incorporated into your ERP system, or a stand-alone application could be used if it is interfaced with the ERP system databases.
- Identifying Picking Mistakes
AI could determine if two very similar items that are stored right next to each other have been causing picking mistakes, and if so, what the scope of the problem would be if the arrangement remained incorrect, e.g., ½” EMT fittings and ¾” EMT fittings. (Based upon my experience, warehouse picking mistakes occur more often than many distributor principals and executives realize.
They could represent between 50 and 75% of mistakes!) Utilizing bar code scanning does not always prevent these mistakes; almost all of my assignments have been with distributors utilizing bar code scanning and are unhappy that their investment has not prevented mistakes).
Three types of data in the ERP system are needed:
- item location(s) – for each item, its ID code and its aisle, bay, shelf and slot location IDs
- adjustments data from each cycle count during the prior “n” months (12 or other larger number) OR from the most recent physical inventory
- credits issued during the prior “n” months; “n” months of data for write-offs — if the data contains a code indicating that the write-off was due to sending an item(s) by mistake AND contains ID codes of the item(s) that were credited because the customer was told not to return them.
Calculating Side-by-Side Picking Errors
The use of inventory adjustments data will work only if each product code contains “body” digits that are the same for all similar products; other digits could designate manufacturer and color/size/capacity. AI would search the adjustment data and determine if there are two or more items with the same body code and similar color/size/capacity; and for each pair, if there was a write-off for one and a write up for the other – an indication that the one written up should have been shipped but the one written down was shipped by mistake. (The adjustment quantity for one item may be different than the adjustment quantity for the other because an unwanted item stored far from the other was erroneously picked).
If a dual adjustment was made for that pair, AI then determines if the two items were stored next to each other or “y” (e.g., 2) slots away; if so, AI would use “n” months of credits data to calculate the value of the credits issued because the wrong item was picked. AI would go on to repeat the steps for the remaining unanalyzed items in the adjustment data, and generate a message showing the time frame, and value of the credits for each item credited, and recommending that each item be stored at least “z’ (e.g., 3) slots way from the other in the pair, and show the total value of credits in the time frame.
AI could also use the credits data to project the value of credits in the next “x” (1 or any other number) period(s) for each item and in total; and generate a message showing the projections. AI uses the same formulas used to project sales. (Note that the value of credits does not include the cost of handling a return of the wrong item and picking, checking/packing and shipping the item wanted in the first place – or the value of sales lost because it was too late to send the wanted item.)
- Reduced Productivity
AI could determine if the storage pattern of items is wasting money during put away and picking, and perhaps result in more picking errors. When productivity is depressed, pickers and others need to hustle to fill orders on time, which often leads to mistakes made while rushing.
Calculating Put Away Cost Inefficiency
Several types of data in the ERP system are needed: item location(s) – for each item, its ID code, velocity code and its aisle, bay, shelf and slot location IDs; “n” months of unit item movement data — number of receipts and number of picks for each item.
Also needed is data that is rarely stored in an ERP system: in each aisle, the average distance from center of the 1st bay to the center of each other bay in that aisle (call it D) and the ID numbers of bays in which “A”-velocity items should be stored (call them As); average walking speed (feet per hour) for put away and for picking; average hourly cost for a warehouse worker – wages plus all benefits, including bonuses.
For each “A” item, AI would determine if its storage location is not in any of the A-bays of any aisle, and if so calculate the distance wasted during picking, which would be approximately twice the distance between its current storage location and the average location of the A-bays in that aisle (which is where “D” comes into play). When the distance wasted is divided by the average walking speed, then multiplied by the average hourly cost, the result is the money wasted per pick. AI would then multiply that waste by the number of picks in a period (e.g., a month), and the result is the money wasted per month.
To calculate the money wasted for put away for each item in question, AI would multiply the money wasted per pick by the number of receipts of the item in that period.
Improving Operational Efficiency Without AI
AI is aways off for most distributors, so until AI becomes a reality, and integrated into warehouse management systems, here are two tips for achieving high warehouse accuracy:
- Identify very similar items that are stored next to each other and move one of them at least two slots away; if practical, move it to another shelf.
- Create a list of fast-moving items and use it to walk the warehouse and note the location of each item with respect to the checking/packing area: aisle, bay, shelf, slot; and note whether that storage location is too far from the checking/packing area.
For more warehouse management tips and tricks, give me a call and we can discuss.”
Dick Friedman helps electrical and lighting distributors prevent warehouse mistakes. He does not sell systems, software or warehouse technology. Contact him at 224 723 5143 or via www.GenBusCon.com for a FREE consultation or more information.
With distributors facing labor challenges – recruitment, retention / turnover, training, increased cost – but warehouse operations being critical to the ethos of what of distributor is, as well as core to ensuring customer satisfaction, it’s important to seek strategies to ensure efficiency while improving productivity. Dick’s tidbits, as well as his suggestions on how AI could help improve warehouse operations, can help distributors improve output, reduce error rates and improve profitability.
Published with the permission of Channel Marketing Group
More information available here